成形不良「シルバーストリーク」の対策
シルバーストリークとは
成形不良の一つにシルバーストリーク(以降、シルバーとします)という不良があります。
水蒸気や、ガス、空気が高温で溶かした樹脂の中に混入して、製品面に銀色のすじ状となって現れる現象です。
プラスチック成形業界では、よく目にする悩ましい不良の一つです。
このシルバーは、突発的に発生することが多く、製品検査でも注意が必要な不良です。
溶けるときにガスが発生しやすい材料もありますが、その他にも色々な要因があります。
今回は、考えられる原因と対策をまとめてみました。
専門用語が出てきますが、ご容赦ください。
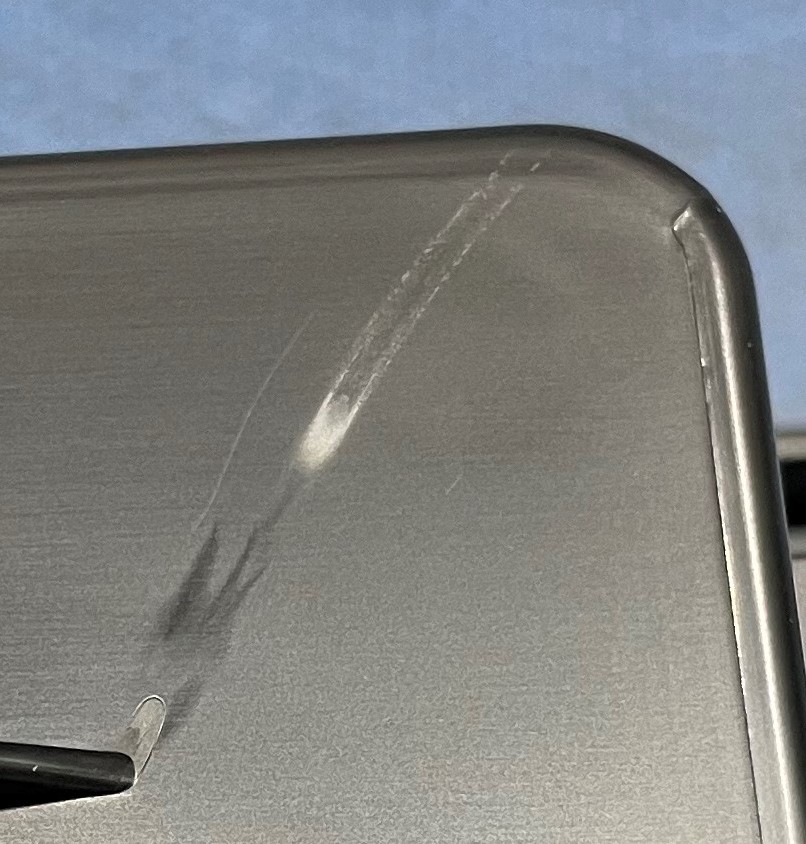
なぜ発生するのか
発生原因について一覧で簡潔にまとめたものが以下の表です。
それぞれ解説していきます。
原因 | 対策 |
---|---|
材料の乾燥不足 | 予備乾燥条件(温度、乾燥時間)を確認し、適正な乾燥を行う |
シリンダー内での滞留による樹脂分解 | ・シリンダー温度を低めにする ・スクリュー回転速度を遅くする |
金型内での空気の巻きこみ | 金型にガス逃げ加工を行い、ガスの逃げ道を作る |
サックバックによる空気吸い込み | ・可塑化完了前のスクリュー回転数と背圧を下げる ・サックバック速度を下げる |
原因① 材料の乾燥不足
成形材料には適正な乾燥温度と乾燥時間が決められています。
乾燥が十分にできていないと、材料に含まれる水分が材料が溶ける際、水蒸気となって泡になります。
この泡がシルバーになります。
ただ、一般的にはどの成形屋さんも、「乾燥温度と乾燥時間」は適性に設定されていることが多いかと思います。
そのため、突然シルバーが増えた場合のとき、乾燥機の故障や、乾燥設定ミスを疑います。
[対策]
予備乾燥条件(温度、乾燥時間)を確認し、適正な乾燥を行う
原因② シリンダー内での滞留による樹脂分解
樹脂には適正な成形温度があります。
この温度が高すぎたり、シリンダー内で滞留する時間が長いと、樹脂の分解が始まり、気体が発生します。
分解しやすい樹脂は、温度と成形サイクルに注意する必要があります。
[対策]
・シリンダー温度を低めにする
・スクリュー回転速度を遅くする
原因③ 金型内での空気の巻きこみ
ボスや、製品形状的に段差がある場合は、射出時に角部に空気が残りやすく、シルバーに繋がることがあります。
複雑な金型形状の場合や、ガスが発生しやすい材料を使っている場合は、このパターンが多い印象です。
弊社でも金型にガス逃げ加工を後から加え、シルバー発生の抑制を行うケースは多いです。
[対策]
・金型にガス逃げ加工を行い、ガスの逃げ道を作る
・射出速度を遅くする
原因④ サックバックによる空気の吸い込み
サックバックの量が多いと、減圧でノズル先端から多くの空気を巻き込むことがあります。
サックバックの量が少なすぎると、ノズルからの鼻たれに繋がり、バランスが難しいところです。
[対策]
・可塑化完了前のスクリュー回転数と背圧を下げる
・サックバック速度を下げる
一つずつ検証することが大切
色々と書きましたが、どのように樹脂にガス類が混入したか、特定するのは実際には難しいです。
複数の原因が関係しているケースもあります。
そのため、実際は対策を一つずつ試して、効果を検証していくことが大切です。